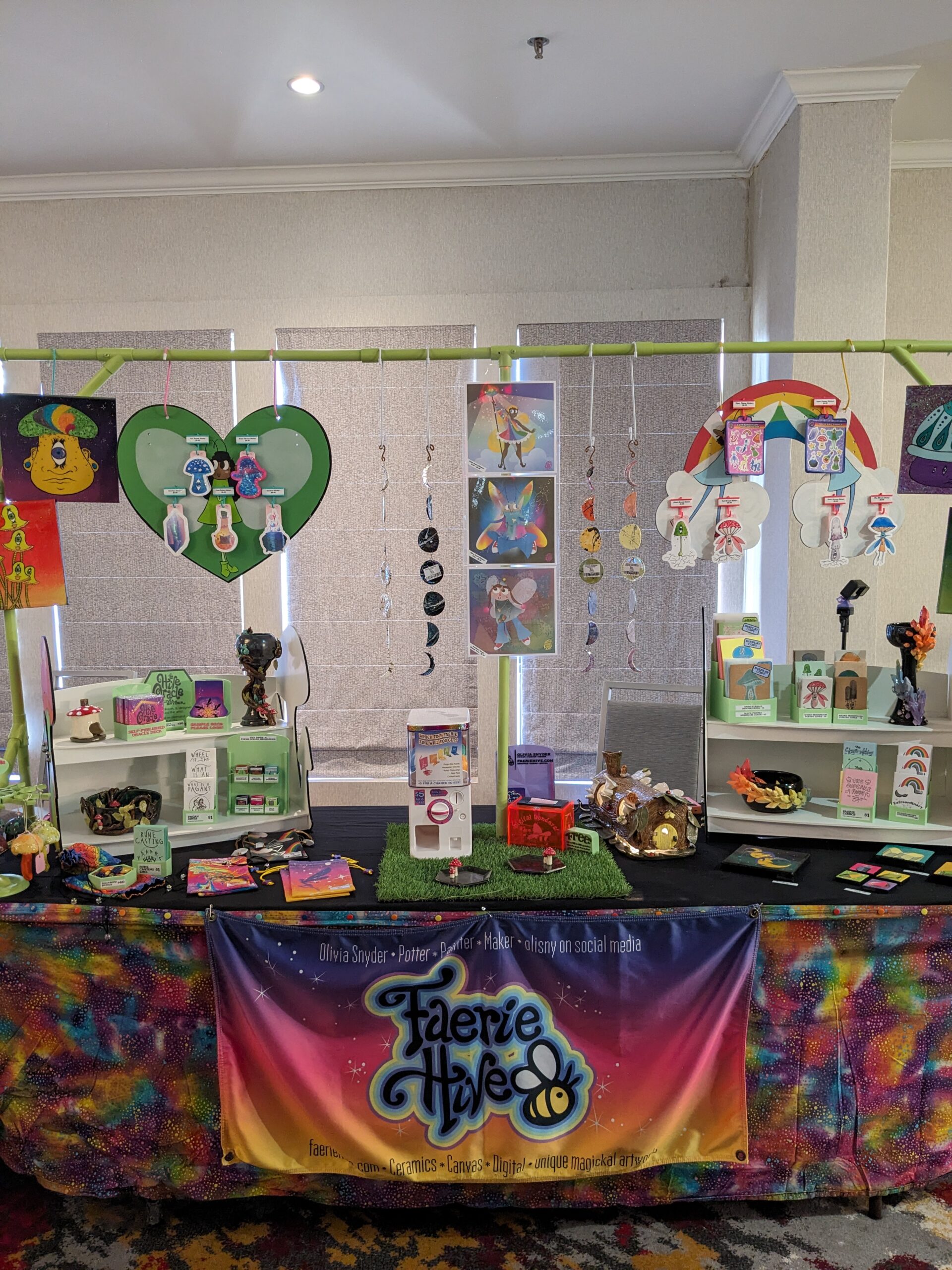
I am here in the dealers room from February 23-25! FenCon is at the DoubleTree by Hilton in Dallas. See you soon!
I am here in the dealers room from February 23-25! FenCon is at the DoubleTree by Hilton in Dallas. See you soon!
The end is coming! Of the year that is har har har. I’m restocking some of my tiny zines for Saturday the 16th, the Misfits Market in Arlington. It honestly blows me away how people have responded to my tiny zine spells and poetry this year! It’s humbling and delightful at the same time, that coming back to paper arts after so long has been positive.
Did I mention? I’ll be tabling at Paper Dragon in Austin on November 18th! It was a tiny joy every time someone bought a faerie egg with a tiny faerie zine inside, so of COURSE I’m stocking my egg machine up with them. 🙂 A new FAERIE COMIC will also be available for the first time in a while. Eeeek! I’m so excited! I hope to see you there~
#zines #gashapon #making #3Dprinting #stickers #faeries #magick
The BANE of my online shop existence is shipping. It’s NOT intuitive, and shipping calculators don’t really account for “a bunch of extra padding that makes this item an inch bigger and an ounce heavier”. That being said, it was brought to my attention that my shop was charging outrageous shipping prices. I had no idea. I try to keep up with it, but stuff gets by me. It’s given me a HUGE pause, wondering how many people put something in their cart, only to be immediately put off by a $60 charge for mailing three zines. The absolute horror.
I HOPE that my day of tinkering, measuring, weighing, and categorizing has fixed this issue. If you’ve ever come across exorbitant shipping charges in my shop, please know that while I cannot afford to offer free shipping, I do my best to keep things reasonable, even if betrayed by the computer! As always, local pickup is free, and don’t hesitate to let me know if you think a shipping charge is way too high, even for pottery. 🙂
Spells? Meditations? In teeny tiny form? I’m working on a big ol’ restock just in time for ArtsGoggle and DFW Pagan Unity! Now with more Solar Eclipse Energy ~ 🌚
So, one of the reasons I call myself a “maker” is because I truly derive joy from the creation and process of bringing new art into the world. I’ve always had a soft spot for printmaking because of the involvement of process.
One of the “cute” methods of printmaking I’ve always had my eyeball on is that of Print Gocco, a now-defunct process for making handmade greeting cards. It was largely for the Japanese card-giving market, and ultimately was killed off by the rise and affordability of desktop publishing. The parent company, Riso, eventually ceased production of not only the device, but the consumables required to actually produce cards/prints. My misfortune was to discover the existence of Print Gocco a mere year after the system’s demise. I never actually acquired a Gocco system because, why? It might be a nifty novelty, but then becomes a dust-collection trinket in my studio after all consumables are gone.
Fast forward to 2017, when I discovered an insanely valuable tool for my maker’s toolbox, 3D printing. I still had the idea of Print Gocco: a cute, tiny print-production studio. I drew up designs to create one using LED lights and small photo emulsion screens to make little screenprinted cards. It kinda fell by the wayside, never to come to fruition, mostly because of how irritating getting materials for the “occasional” screenprint became. I’d have to buy enough emulsion to coat something like 20 giant screens, but it seemed such an absolute waste when I ended up making two tiny screens for cards or ceramics. Emulsion doesn’t last forever.
Last week, I randomly decided to poke into the world of Print Gocco again. I wondered if the system was easier to get? Maybe someone was making bootleg supplies? What’s up? I stumbled on a great blog post on No Bad Memories discussing a deep dive on the Gocco process. Long story short, the dots were connected for me that Print Gocco was made by the same company that owns the Risograph, the Riso Kagaku Corporation.
I love making zines, and haven’t been able to find a place in DFW that offers Risographs to the general public. Oh, I’m sure there’s a place out there, but I haven’t found it yet. In the meantime! Thanks to No Bad Memories‘ additional blog post, I’ve put my mail label printer to work and have made my first two-color print using a method related to Print Gocco.
Unlike screenprinting, Print Gocco uses heat to essentially burn away a thin plastic film from a super-thin fiber substrate. No Bad Memories uses a label printer to accomplish this, another source, Stampalofi, uses a repurposed thermal fax machine to do so.
It took me a bit of experimenting to find settings that worked for me, but here’s a little rundown of my process, may it help other people also interested in hand-making little mimeographs. I highly recommend reading both of the blogs on No Bad Memories, in addition to watching Stampalofi’s videos if you’re unfamiliar with the process.
The name of the magical material to make stencils is typically referred to as “Risograph master”. You can find rolls of this on eBay for at various price points: I got lucky and snagged a roll for $13 including shipping. (Generally they seem to go for around $50 for 2+ rolls. Shop around.) This gives me enough material to make literally hundreds of cards. It is essentially a roll of super-thin tissue with a super-duper-thin layer of plastic. You will want very sharp scissors/blades/papercutter to cut this stuff.
Me, I have a Munbyn label printer. They’re not too expensive, and super handy when you have to make thermal stickers like mailing labels and bag labels for your small business. The label printer prints via heat, not ink. Thus, it is perfect for this project.
I’ve screenshotted the settings I have found to work: yours may be different! But in my testing I’ve found that you want the label to go slow enough to allow for the plastic to burn away, and a power level in that Goldilocks area of not too hot and not too cold. Too hot will melt too much plastic and you’ll be scraping melted plastic off the heat element of your printer.
Color! This biggest issue with screenprinting is you don’t want your inks to dry on you. In big boi screenprinting at the factory, a lot of inks need to be heat-dried, so they don’t dry superfast. Fancy pants artists often use oil-based inks to print. I phased out all oil-based materials in whatever I’m doing because it smells terrible, gives me a headache, and is a PITA to clean. For our little Print Mocko, we want something that gives us working time and won’t dry faster than we can print. Stampalofi has a great video on making nori paste to extend the working time of acrylic paints. However, if you have them available to you, Speedball’s Block Printing Inks have a moderate working time and are water clean-up. They worked perfectly for this.
A block print roller or brayer. Screenprinting uses a squeegee. I started out using a squeegee for this, but it was MUCH too aggressive for the delicate fiber stencil. I noticed it breaking down after a short while. Finding inspiration from devices like the Edison Mimeograph, I found that using a roller was much better suited to the process. Again, Stampalofi has a great video on using a Lion Menucator, which illustrates the hand-rolled Mimeograph. (If you’re a huge dork like me, check out this filmstrip on “Mimeographing Techniques“. Yessir, us old folks remember getting purple copies in school for our worksheets.) In short, a hard rubber brayer worked great.
A frame of some sort. In my pictures, I used one of these I obtained at Daiso for cheap and cut it up. (Believe me, I’m mulling on how to best over-engineer a reusable 3D printed solution.) For an even cheaper solution cut up an old cereal box and tape your stencil to it.
Paper. You can’t used a toothy/textured paper for this. You’re not gonna get a clear impression. Use something smooth. For this project, I used some generic cardstock I got at HEB. My proofs were done on index cards. Entire project was great for the wallet-area.
This isn’t an especially detailed tutorial, rather an overview of my process after I manufactured a stencil. I will reiterate that 1) I’m assuming someone endeavoring to make lil’ mimeograph prints is familiar with the general idea behind risographs/mimeographs and B) has checked out linked blogs.
Checking fits with my Daiso frame I made. The plastic is soft enough to bend a bit, but stiff enough to provide a nice frame for the stencil to fit into.
In this shot you can barely see where the plastic material has been burned away. Crucially, you will need to do two things when running the stencil material through your printer:
Evidence of squeegeeing/scraping the ink through the stencil. The entire setup being clear was helpful with half-assed registration.
Lots of little one-color prints! Embrace the lil’ imperfections, for they are what exposes your laziness humanity.
When you’re done with a color, so is your stencil. My aggressive squeegeeing absolutely wore it out, and removing it from the frame completely destroyed it.
After a bit more scraping, I switched to the brayer. The results were MUCH more satisfactory, not to mention less messy. The next project will be brayer-only.
Checking a proof of brayer use. MUCH easier.
Look at all those imperfections! Things definitely crisped up after the brayer. Using the squeegee, you can tell where I was afraid to scrape and ruin the stencil, resulting in less ink deposited.
Mmm…so printy. This is pre-signing and edge-rounding. After that, they will be released into the wild as free art!
This entire Print Mocko project satisfyingly scratched an instant gratification itch I get now and then. (Pottery is NOT a speedy process!) I can’t wait to experiment with using the Riso stencil material for ceramics, and incorporate some spot colors into my zines.
A condensed list of helpful sources:
I’m grateful to those who have shared their techniques, sources, and information in keeping old technologies alive in some form or another!
So, I picked a very heavy craft to follow. Pottery isn’t exactly light, and I tend to get extra fancy with my displays. For about 10 years I was a face painter at various conventions, birthday parties and what have you, sadly, that did a lot of damage to my back. When you’re in your early 20s, you tend to not fuss yourself with “old people” problems like taking care of your back.
Come Fall of 2022, my second-to-last show of the year, I put my back out lifting boxes of pottery and equipment into my car, and hauling it to the show site. The phrase “I’m too old for this” has never repeated itself over and over so many times in one head.
I needed a way to showcase and move pottery to shows that didn’t murder my body.
Ever since I first saw Andrea Denniston’s Teardrop Build, I became enamored with the idea. Stash everything inside? Hell yes. Trailer becomes display? More hell yes. Similarly, I loved Diana Kersey’s “Foamie” display trailer after seeing it at Texas Clay Festival. No tables to haul, no shelves to assemble, just stow and go. It’s like an infomercial.
Planning commenced, with minimal self-imposed stipulations:
The venture into Trailer Land began with installing a tow bar onto the Subaru. The resources at E-Trailer.com are great, they have clear instructional videos that allow you to not pay $200+ at U-Haul to have them install a tow bar as was recommended by far too many people.
Use that $200 towards a Harbor Freight trailer frame. I picked me up one of these bad boys for a little over $400. Buying new, it was the cheapest. Had I shopped around, I might’ve been able to pick up a good second-hand trailer for a reasonable price. My reasoning was that building it would give me a better understanding of how the thing worked. Plus building stuff is fun.
I wasn’t especially sure how well me and the trailer would get along, so it went on a “test trip” to an event in Austin with all my equipment, sans pottery, strapped to the back. The only thing I added was a 3/4″ plywood floor.
Strapped on were my three display tables, tent, box with tent roof/walls, and box with display shelves. (Shelves flat pack.)
At this point, I was too nervous about the leaf spring shocks providing any protection to my pottery, so it traveled in the car.
The inaugural voyage got me used to pulling a trailer of stuff, how it moved, and the fact that I cannot for the life of me reverse the car and get the trailer to reverse.
It WOOD (haha) have been great to be able to find lots of salvage and build with it. But I live in a post-apocalyptic suburbia where people charge a premium for garbage fence pickets on NextDoor. Fortunately, I had plenty of my own scrap, PLUS a retired bed platform I had constructed about a decade earlier. This isn’t to say I didn’t plunk down a chunk of change on new wood and needed hardware; you can only dig so much out of your personal woodpile.
No, I did not follow any specific building guidelines. I eyeball a dangerous amount of measurements, though in general rulers and cuts weren’t too wonky.
At this point, the majority of the construction was done. Originally, I had planned to put shelves on hinges that latched up, so I could pull up to an event, unlatch the shelves, and boom. Put up pottery. However, after a test run, I was concerned about the amount of rattling and jiggling outside shelves would take.
I took the base on a test run throughout the neighborhood, doing my best to emulate MarioKart. Topped it off with some donuts in a school parking lot, and I was satisfied that the house wouldn’t tip, and had no tendency to lean one way or the other.
I decided to go with French cleats for hanging my shelves. That way I could add more, put up less, and not worry about them becoming damaged while in transit.
French cleats are pretty reliable as far as holding weight, but mine were kinda skinny, so I added tabs to prevent horizontal motion from happening. Unless someone trips and falls into the house, it ain’t goin’ no where. The brackets pop off for transit and ride inside the house with the shelves, all is well. Each bracket took around five hours, I printed two at a time, each side had eight brackets. My calculator tells me that’s roughly 240 hours of print time. That comes out to…TEN DAYS to print the brackets. Man. My Prusa needs a vacation.
At this point, the Texas weather was unseasonably warm for days at a time. This means it’s time to start slappin’ down paint!
UGH I forget how much painting solid colors sucks. This step not only involved painting, but also patching, caulking, sanding, etc. The WOOOOOOOOORST. You only THINK you bought a decent piece of plywood until you have to paint that sucker. Then you decide your next project will be to go back in time and hit yourself with a bag of cement for picking the world’s lumpiest, bumpiest, most uneven sheet of wood known to mankind.
I wanted shingles for the roof. I looked. And looked. For some crazy reason, people only want to sell you enough shingles to get started covering an entire regular-sized house. People building 4′ x 4′ homes need shingles too, people! After more dead-ends than I would’ve liked, I printed out a test leaf-shaped shingle.
Test leaf came out perfectly. I liked the shape, I liked the look, and it had the unanticipated benefit of being able to be shaped by heating it with a heat gun. I guess we’re doing this. Rough calculations say we’ll need…SEVENTY TWO LEAVES to cover the roof. Time for a trip to Microcenter, I guess.
Each leaf took two hours to print, not counting the time spent manually changing filament colors. (I even cobbled together some gcode to make it spit the filament back out at the end of a print to save me that step.) You get out your own calculator to figure out how long the print time was for the leaves because SIX DAYS OF PRINTING GOOD GOD
I really need to do some printer maintenance.
Next is fun painting. Still laborious, but fun. Barring cold days, it probably took around two weeks to get all the painting done. I opted to go with regular ol’ craft store acrylic paint as A) the trailer would not be sitting in the sun for months at a time causing fading and B) the entire trailer would be getting a clear coat of polyurethane.
Because the weather was warm/cold/warm/cold, I spent some time doing a bit of 3D printing during the cold. First up, a nice plaque to go over/in the sun on the back of the house.
Have you ever struggled with cutting angles beyond 45° with wood? I have a miter saw and a desire to keep all my fingers, so I couldn’t figure out how to safely cut wood slats for the gables of my little house. 3D printing and a protractor to the rescue! I measured, printed, and got close enough to say “Eh, I’ll fill it in with caulk.” Tada, fake gable supports.
Back to painting! I like my faeries to have transparent wings, so I did a little airbrushing and cut some wing stencils in order to spray on some color-shift paint for wings. Violá! In the meanwhile, I started to add some black to the roof and trim.
Time for…a freeway test run. I’m a member of a makerspace in Richardson, TheLab.ms. Folks on our Discord channel kept asking me how it did on the freeway. My builder sister asked me how it did on the freeway. My experienced father asked me how it did on the freeway.
Uh, I suppose I need to take it out on the freeway.
Opting for a Sunday evening drive, I tooled my not-quite-finished trailer out to TheLab and lo, I arrived safely. Much trailer building discussion was had, and I made it back home in one piece. Huzzah.
Back to painting!
Oh. I guess that was a short rest of photos documenting painting.
Painting, DONE. Time to add on the cleats and hang the brackets and place the shelves!
The bottom shelves were a bit of a concern; I wanted them to cover up the wheel wells, and “frame” the house. However, they’re right at knee height, and if someone were to bump them a bit, they might tip. The brackets weren’t enough for how wide I wanted them. Simple solution? I drilled a hole and put a clevis pin through the shelf and wheel well. Shelf isn’t tipping nor is it sliding, and the pin is super fast to install.
I was a bit concerned with visibility at night despite looking like the Studebaker from the Muppet Movie, so I managed to locate some reflective vinyl online. Five minutes on the Cricut later, I had a jumble of lettering to adhere to the house.
Not all the vinyl is reflective, just the giant-ass website so people know who to complain to when I cut them off.
I admit I was waffling on the leaf shingles up until two days before I had to leave for a show in Austin. Would they hold up under three-ish hours of sustained 75mph winds? Did I want to test that? I had screwed three leaves for my test drive to the makerspace, but not an entire roof full.
Screw it, I’ll put ’em all on.
Using the heat gun to bend the leaves brought an unexpected benefit; it basically fused some of them together, thus eliminating potential flapping in the wind. I lost a few leaves, but way less than expected. Fortunately, it was not noticeable at the show.
Time to play trailer Tetris! Load ’em up! Pack it up! Cram it in! Pottery this time rode in the trailer, tightly packed in with packing foam. Everything else was strapped down with either bungees or straps inside.
The top of the car had to hold the tent. It’s just too long to fit into the house! Likewise, I was concerned about my larger ceramic faerie houses being banged around too much. They’re not packed especially tight, and I felt better with them in the back of the car.
Overall, I’m absolutely pleased and satisfied with this build. It was challenging, used a variety of my skills, and was extremely eye-catching in its final form as a display piece.
Will there be future improvements/additions? Absolutely. But my major goal was to create a transport and display that wouldn’t kill my poor back at the end of the day. I’d say I nailed it.
Addendum: 72 leaves were not enough, nor were 90. I suspect I’ll have to update later with exactly how many leaves create a satisfactory roof.
I am super-excited to announce the official release of my very own oracle deck, the Hive Oracle! This is truly a labor of love. The deck consists of 34 cards of vector-illustrated faeries, imps, sprites, witchies, and wands, by me. This deck isn’t so much focused on fortune-telling as it is on personal examination using elements many pagans are familiar with. Utilizing a unique hexagonal shape, the deck can allow for a spectrum of answers rather than a solid “yes/no” answer.
Currently the deck is available as print-on-demand from the company I am self-publishing from, The Game Crafter. I’m impressed by the quality of the cards, the box, and the booklets! Everything is printed and manufactured here in the USA, so you don’t have to worry about shipping delays from overseas. Keep an eye on special items to go with the deck, coming soon: a reading cloth, hand-sewn bags, and the complete printed manual. In the meanwhile, all information and instructions for the deck are available here on my website!
Happy Equinox! Texas is delightful right now, bright and sunny with fresh green popping up everywhere! The studio is in full-swing with producing pottery for Artscape at the Arboretum. April 24-25, I can’t wait! In the meanwhile, I’d like to share with you a commission that was an absolute joy to work on during 2020. This was painted for a dear friend who covets a Constellation Thai Monstera, but, alas, they are incredibly expensive at the moment. Thus, the Monstera Faerie now graces her walls, chillin’ out on a plant that never needs watering. I hope you enjoy it, too!
Goodness! It’s been a while, eh? This year has been a doozy, and I’ve had my own share of “How in the world do I deal with this?” moments. Every single show I had on the docket for the year has been cancelled, sadly. I love going to shows! I love meeting people and making things that make them happy. The moment someone finds “their” mug or plate is a precious moment of joy for me. It’s a delicate balance of staying positive for next year and trying to stay grounded in reality. I’m sure most people can relate to that!
Because I suddenly find myself with no shows or festivals to prepare for, I’ve turned my attention to a project that’s been on the back burner for years: an Oracle Deck. We’ve entered the harvest season, and I’m starting to see the fruits of my planning and drawing. I share with you a collage of in-progress photos: sketches, prototypes, computer drawings, lists of drawings to complete. It is my goal to have a finished product in-hand before the holiday season!
I hope that all folks are doing well during this tumultuous time: the wonderful thing about the world is that it’s natural state is of one in balance. May you find your OWN balance and peace.